一、概述
普通磨削的砂輪速度常在(30~35)m/s之間。當砂輪速度提高到45m/s以上時,則成為高速磨削。將砂輪速度由35m/s提高到(50~60)m/s時,一般生產效率可提高30%~100%,砂輪壽命提高約0.7~1倍,工件表面粗糙度降低約50%,可穩定達到Ra(0.8~0.4)μm。
高速磨削的特點如下:
(1) 在一定的金屬切除率下,砂輪速度提高,磨粒的當量切削厚度變薄。因此:①磨粒符合減輕,砂輪的壽命提高;②磨削表面粗糙度降低;③法向磨削力減小,工件加工精度較高。
(2) 如果砂輪磨粒切削厚度保持一定,則υs提高,金屬切除率可以增加,生產率提高。應用高速磨削須采用的措施如下:
1) 砂輪主軸轉速必須隨υs的提高而相應提高,砂輪傳動系統功率和機床剛性必須滿足要求。
2) 砂輪強度必須足夠大,還應經過平衡及采取適當的安全防護裝置。
3) 采取有效的冷卻及防磨削液飛濺裝置。
二、高速磨削砂輪選擇
高速磨削除要求砂輪具有足夠的強度以保證在高速旋轉時不致破裂外,還要求砂輪具有良好的磨削性能,以獲得高的磨削效率、壽命和加工表面質量。我國已生產有60m/s、80m/s的高速砂輪。
1.砂輪特性的選擇
(1) 磨料的選擇。主要選用韌性較高的剛玉系磨料。其中棕剛玉A應用較普遍,用于磨削一般碳鋼和合金鋼;磨削球墨鑄鐵材料時多用A與GC的混合磨料。
(2) 粒度的選擇。粒度大多選用F60~F80,較普通砂輪粒度偏細。一般精磨時,宜選F70或F80,有利于提高砂輪的切削能力和壽命。加工塑性材料及避免工件表面燒傷時,宜采用粗一些粒度。當υs≥80m/s時,粒度宜選F80~F100.
(3) 硬度的選擇。高速砂輪的硬度比普通砂輪稍軟一些,一般在K~N范圍內。精磨時宜選更軟一些;余量大或粗磨時宜選硬些。對于磨削一些不平衡的工件(如凸輪軸、曲軸等),由于不宜提高工件轉速來減少表面燒傷,砂輪硬度應適當選軟些。
砂輪的硬度和粒度,還與砂輪可能達到的破裂速度有關,如下圖所示。隨著硬度的提高,同時選用較細的粒度,則砂輪破裂強度相應提高。

砂輪破裂速度與砂輪硬度、粒度有關
(4) 微氣孔砂輪。高速磨削時,因進給量加大,砂輪粒度較細,因此要求砂輪表面上有一些微小氣孔,以利于磨屑與磨削熱的排除,使磨削效率和砂輪壽命得以提高。但氣孔不能太大,否則易使磨粒不均勻脫落加劇。
1. 提高是砂輪的強度
提高砂輪強度,可通過下述方法實現。
(1) 改進結合劑。為提高結合劑的強度,在陶瓷結合劑中多采用硼玻璃等結合劑。
(2) 砂輪孔區補強。砂輪旋轉時最大拉應力位于孔周壁上,最初的破裂是沿周壁發生,所以采用孔區補強是提高砂輪強度的有效方法之一。常用的砂輪補強措施如下圖所示
圖(a):砂輪孔區部分采用細粒度磨粒和較高的砂輪硬度,砂輪強度可提高20%~25%。
圖(b):孔區部分深入補強劑(樹脂液),通過孔周壁滲透到砂輪內部。用此法砂輪強度可提高5%~15%,氣孔率大的砂輪強度提高得更多。
圖(c):用一金屬環粘結在砂輪孔區,金屬環可用鋼或耐熱合金制成,用環氧樹脂等與砂輪粘結。
圖(d):是樹脂砂中加玻璃纖維網。
圖(e):增加砂輪孔區厚度和圖(f)用法蘭盤裝夾提高孔區強度。這兩種方法多用于薄片砂輪,效果明顯,對厚砂輪則意義不大。
(3) 改變砂輪的形狀,以改變應力分布狀況。當砂輪高速運轉時,孔壁處應力最大。但孔徑越小,應力也越小。所以應盡可能采用孔徑與外徑比值(K=rf/R)小的砂輪或無孔砂輪。通常砂輪孔徑與外徑之比不應超過下表所列數值。
砂輪孔徑與外徑之比值K的最大允許值

無砂輪多用法蘭盤粘結或在半徑152mm(視砂輪外徑大小而定)的圓周上開有幾個螺釘孔,用以固定在機床上。
(4) 采用新結構梯形砂瓦組合砂輪見下圖所示。當砂輪旋轉時,砂瓦由受拉應力變為受壓應力,而砂輪材料所能承受的抗壓強度是抗拉強度的6倍,因此這種可在較高的速度下工作。
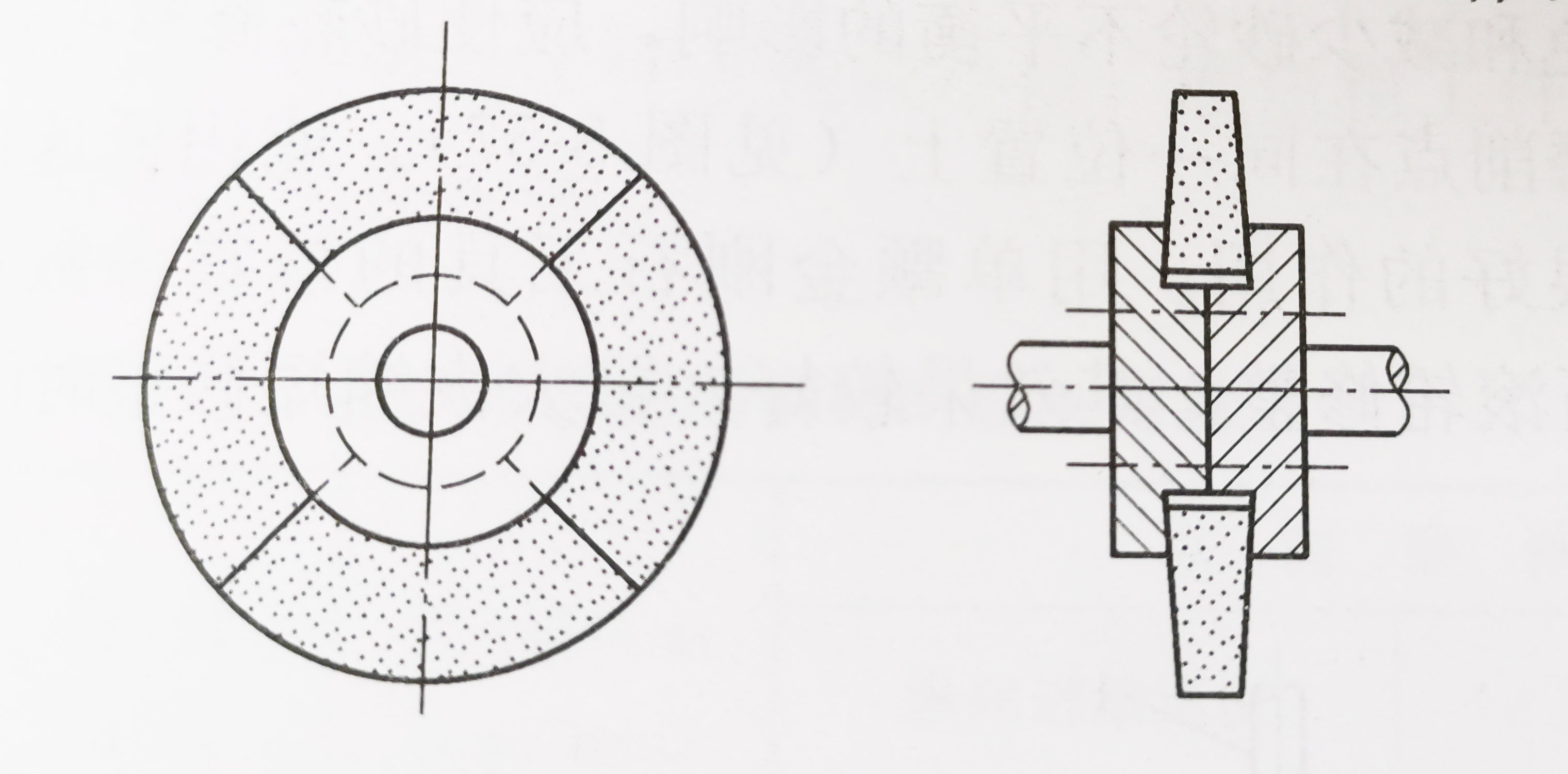
梯形砂瓦組合砂輪
在高速砂輪上必須印有醒目的安全工作速度標志。選擇砂輪時要注意安全系數或嚴格控制υs,不得超過安全工作速度。